干式复合中塑料薄膜遇到的问题
作者:admin 发布时间:2023-02-17 点击量:次
在复合中塑料薄膜出现的小问题如:胶层出现小气泡,复合不牢固、复合成品发硬、热封欠佳等问题,产生这种结果的因素很多,下面就这种情况进行一探讨。
一:胶层出现小气泡
在生产过程中偶尔会出现各类气泡,其实它只是个笼统的概念,它并不一定是真正凸起来的汽泡,
也有可能是两层膜之间未完全贴合,透明度就会有差异,形成我们常说的小气泡。
其产生原因可以几个方面考虑:
1)我们首先要考虑的是不是上胶量不足,实际上复合膜是否进行印刷,
和基材以及胶的表面张力以及涂覆的流平性都反映了上胶量的多少。
2)干燥不良形成的小气泡.
3)堵版形成的小气泡.
4)复合热辊和压辊不平整产生汽泡,不平整的地方带进了气体,形成小气泡.
5)因熟化温度不够,没能消除气泡.
塑料薄膜中出现气泡其实复合膜一下机也就没有气泡,而熟化能消除小气泡,
加热主要是为了使干固的胶粘剂熔化,流动,消除小间隙,在压力之下排出气体,使二层膜紧密贴合。
二:复合不牢固
1)表面张力偏低通常情况下,干式复合用的塑料薄膜的表面张力必须达到38dyn/cm以上才可以使用,
同时复合强度还与塑料薄膜的厚度相关,塑料薄膜越厚,相对塑料薄膜表面张力要求要高,
并且塑料薄膜存放时间越长其表面张力值逐渐下降,同时也受空气湿度和季节的影响。
2)添加剂的影响树脂在聚合或在成膜时,根据其性能的不同,一般都需添加一定量的添加剂,如滑爽剂、抗粘剂等。
爽滑剂以及其它有些改性剂具有可变性。
塑料薄膜放置一段时间之后,爽滑剂会从塑料薄膜内部移迁至塑料薄膜的表面,产生一层很薄的致密层,
这层致密层阻隔了粘合剂与塑料薄膜表面的结合,导致粘合剂无法与树脂接触,复合初粘力很低,
但是在自动包装中,即需要具备高的复合强度,又要求较低的摩擦系数,
为了解决这些矛盾,我们一定要选用耐高温,迁移速率慢的高分子量的爽滑母料,
并且在爽滑母粒的添加比例上,在能够满足一定的摩擦系数前提下,尽可能的少加这类迁 移性的助剂。
3.热封不佳塑料薄膜在需要热封的情况下会出现局部热封不良的现象
导致这种现象主要有以下原因:
电晕击穿塑料薄膜在生产中经过高压放电辊时,由于种种原因可能会导致膜的局部击穿。
测热封欠佳处膜的表面张力值一般都比较高,由于被击穿的热封面与复合面一样形成了含有极性的基团,
部分还出现交联,这些也会影响塑料薄膜的热封性。
爽滑剂的含量偏高是由于薄膜热封层爽滑剂含量成份过高,会导致其大量析出在PE膜的表面上形成致密层,
阻碍了PE膜的热封, 因此在选用在爽滑母粒也要尽量选用耐高温,分子量高,质量好的,
在摩擦系数要求不高的条件下,可以选用非迁移的低摩擦系数的抗粘母粒。
抗粘母粒一般分为无机和有机抗粘剂,主要特征是透明度和光泽度好,微珠状,添加在薄膜之中摩擦系数低等特点。
三:原料选择上要谨慎
热封层一般材料要选择熔点低,热封温度宽,热封性能好的原料,
所以在原料选择上一定要谨慎,不然就会导致热封不良的现象,为节省成本使用再生料,这也会影响薄膜的热封。
四:薄膜的透明性差
1)冷却效果不好流延膜在生产工艺过程中原料经挤出机塑化熔融后,熔体经过模头挤出,
流延铸片经急冷辊冷却,PE、PP都是典型的结晶型聚合物,在急冷的过程当中,结晶速度加快,
从而结晶颗粒微细化以及降低了结晶度进而提升其透明度,所以急冷辊的冷却效果至关重要。
当然在原料加入成核剂也能够提高薄膜的透明度,成核剂可分有机成核剂和无机成核剂两大类。
2)原料和母粒的选择不当薄膜的透明度除了工艺上的控制,在原材料和母粒也有直接关系,
在流延膜生产环节中,为了避免薄膜粘连和降低摩擦系数,必然要加入抗粘爽滑母粒,
不同类型的母粒其雾度和光泽度均有不同,但是为了薄膜的透明度,一定选择雾度低,
折射率和树脂接近的抗粘效果比较好的母粒。
五:复合后成品发硬
干式复合一般采用的是二液反应型粘合剂,复合后要进行高温固化,以达到最高的复合强度,
而PE膜内的爽滑剂往往会因为固化温度的变化而变化,在特定的温度下,
熟化前爽滑效果很好的薄膜熟化后COF变得很高,温度越高,这种变化越大,
这是由于爽滑剂的部分损失和爽滑剂的内迁影响的,最终也会导致产品发涩,无法使用,
所以,我们在控制好熟化温度的同时,一定要使用高分子量,耐高温,高质量的爽滑母粒才能避免。
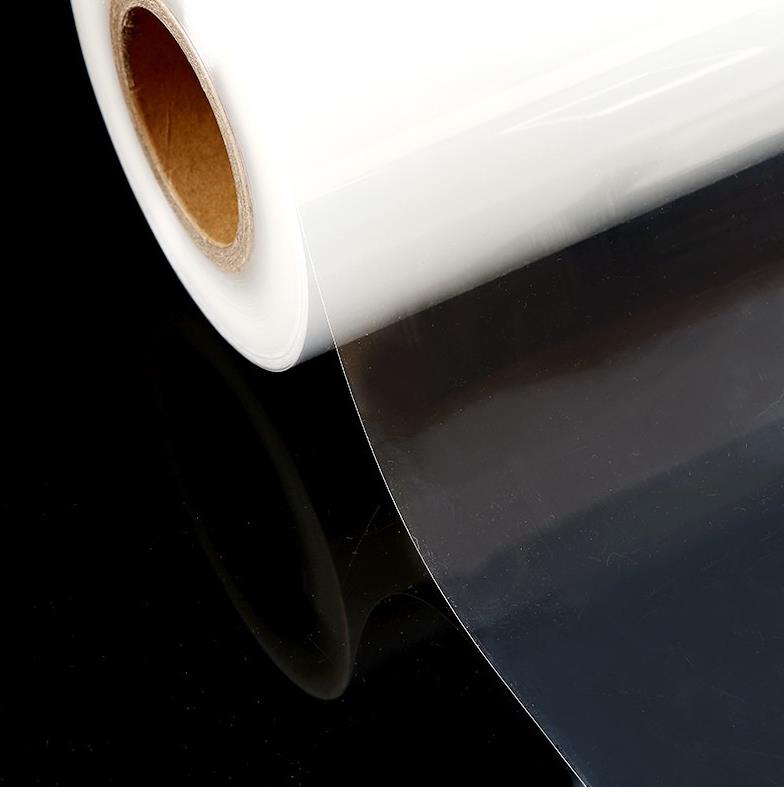
上一篇:evoh阻隔膜基本特点 下一篇:包装膜热封层材质知识,必看这篇文章